Nuclear cost reduction: Learning lessons requires investing in people
Nuclear power is a people business. Through the hard work of many, most plants operate at very high operating factors and produce clean economic electricity 24 hours a day 7 days a week. They produce in good weather and bad, when it is sunny and when it is dark, when it is windy and when the air is still. This was not always the case. It is decades of effort by an industry dedicated to continuous improvement and learning that led to this outcome. Utilities collaborate and participate in groups such as the Institute of Nuclear Operators (INPO) and the World Association of Nuclear Operators (WANO) to ensure that operators have access to industry best practices and then they work hard to implement them at their own plants.
This process of continuous learning has not yet been fully achieved when it comes to building new plants. Here the experience is more regional with some countries like Korea and China having great success, and others struggling with new build projects that have been both behind schedule and over budget. A new report by the OECD Nuclear Energy Agency (NEA) addresses this issue head on. “Unlocking Reductions in the Construction Costs of Nuclear: A Practical Guide for Stakeholders” focuses on both the reduction of construction costs through a selected number of well-defined cost drivers and on the reduction of the cost of capital through the improved allocation of construction and market-related risks faced by new nuclear projects.
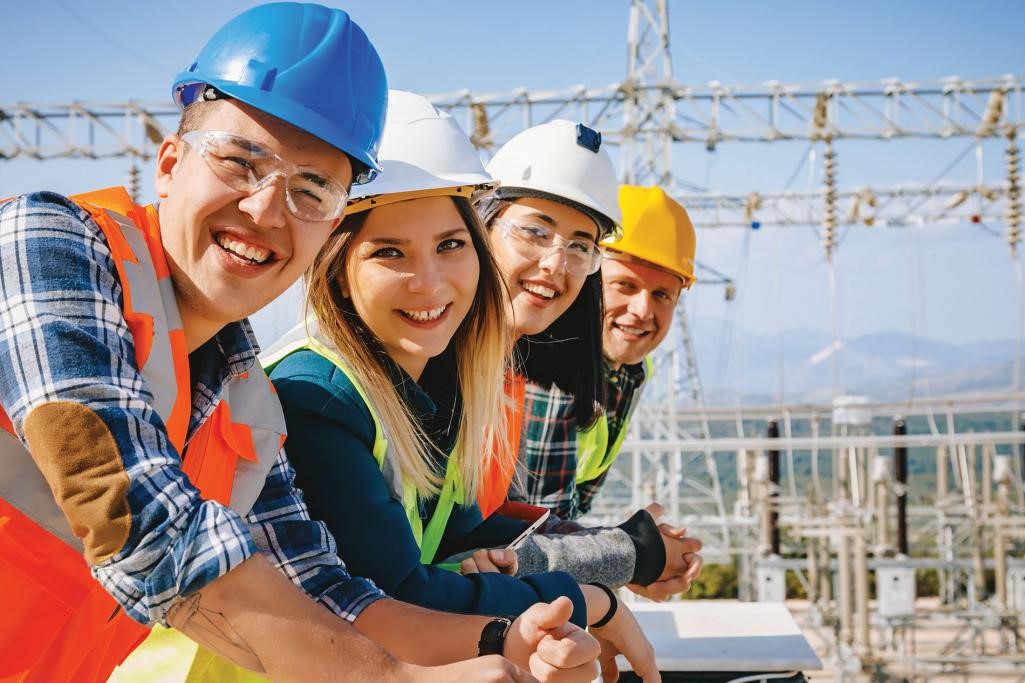
Back in 2018 we posted with our own three-part series on managing nuclear costs. As we noted then, large capital projects are difficult. They require a huge amount of planning, the logistics are often staggering and depend upon many contractors and suppliers, all who must perform completely in step for everything to come together as planned. The project manager is like the conductor of a large orchestra and as good as all the musicians may be – it only takes one misstep to ruin a beautiful piece of music. Strong leadership and good people are the key.
The NEA report focuses heavily on implementing the many lessons learned from existing projects to make the next projects better. As they state, “to reduce nuclear construction costs, eight drivers have been identified to unlock positive learning”.
We have all heard about the importance of having a strong “lessons learned” program. To be truly successful, the meaning of each of these words needs to be fully embraced.
First, we have lessons. These come from the difficulties identified in a project that should not be repeated, or new better ways to do things based on experience in the field. At the end of a project, you may hear there have been many lessons learned that have been collected ready for the next project. In reality, these are just lessons as we don’t yet have any evidence they have actually been “learned” by those who need them most, the people who are going to build the next plant.
“Learned” is defined In the dictionary as acquired by learning, acquired by experience, study. The operative word here is “acquired”. What we so often forget when we talk about lessons learned is that identifying a lesson is only the beginning. What is really important is to ensure the lesson is actually “learned” by the people who need to learn it and then successfully put into practice. We can only know this when the next project comes, the lesson has been applied and the results measured to demonstrate the lesson has indeed been learned with the project seeing the expected benefit.
Yes, new methods can be recorded based on previous projects that will avoid errors and improve project performance. But to really make improvements in project delivery requires the kind of learning that comes from experience and improving individual efficiencies. These lessons are carried by people, not databases. This means that to get the best project results, the same people must do the same tasks over and over again going from one project to the next.
Or as said in the NEA report – “the most effective way to reduce construction costs in the near term (early 2020s) is to develop a nuclear programme that takes advantage of serial construction with multi-unit projects on the same site and/or the same reactor design on several sites.” While it is true there are technical savings building on the same site, the largest savings occur because the use of the same workforce is maximized. As a task is completed on one unit, the same people can use what they have learned and immediately move on to the next unit and repeat the effort. This ensures the largest possible cost reductions.
We can use a simple example from our own lives familiar to us all. Who hasn’t had to do a project around the house and found a video on YouTube to show you how to do the task at hand? What an amazing tool! Yet even with the best step by step instructions from an expert on YouTube, we will still do the job much faster the second time. There is simply an experience factor in everything we do that cannot be easily transferred from person to another.
The path to success is through empowering people, providing them the opportunity to maximize their learning and then make use of this learning to continue to improve project performance. While it may sound counter intuitive, this will also fuel innovation as those with the most knowledge and experience continue to find ways to get even better. This means:
- Standardizing is much more than just repeating a design. It is using the same people who have done the same work (engineers, project managers, suppliers and trades) on the previous project. They know exactly what to do and how to do it.
- Recognizing there are limits to using all the same people for multiple projects – train, train and train some more to develop those that are new to the project. Avoid the mistake of training for competency and train for proficiency. Training must be managed by people who have actual experience. They must transfer not only their expertise but their experience as well.
- When preparing for a new nuclear project, build the experience of as much of your workforce as is practical by sending them to participate in on an ongoing project before they start work on your project. The more people you have who are not touching something for the first time on your project, the better.
Of course, this can only be accomplished with an active new build program. The example of China and Korea and their success in lowering nuclear costs and building to schedule are cited regularly. Their strength is in the size of their programs. We have personally had much experience in working with Korea and we can honestly say, that having been in the industry a very long time, we actually know Koreans who have worked their full careers and have recently retired. Each one of them has worked on a real new build project every day of their 30 plus year careers. This kind of experience is invaluable and is why their projects have continued to improve. In the western world where new build has been paused, who can say the same?
Remember, when we talk about lessons learned, the operative word is “learned”. All the lessons in the world are of no value unless this knowledge is acquired by people and put into practice. This means collaborating to develop capabilities and install a system of continuous learning throughout all aspects of the industry, just as we have done to improve nuclear operations. After all, we only need to look at global nuclear plant performance to know this works.
This is an industry that attracts the best and brightest. Let’s give them the tools to acquire the knowledge they need, and more importantly, lets offer them exciting careers to develop the experience required to build the nuclear future we all aspire to. We have so many great lessons available to us; now let’s put the emphasis on learning them.